What is Concrete Batching | Types of Concrete Batching | Concrete Batching Plants
Concrete is the most often used construction material in the world because it is adaptable, strong, sustainable, and affordable. The percentage of the elements for concrete must be measured correctly and precisely to produce a product of outstanding quality. By performing the batching procedure, the ingredients for concrete may be measured precisely. To make the concrete mix, a procedure known as batching determines the quantity or percentage of ingredients such as cement, aggregates, water, etc. based on either weight or volume. In this article, we will try to understand concrete batching, types of concrete batching, and concrete batching plants.
By minimising segregation or bleeding in concrete, proper batching enhances its workability. Having a smooth concrete surface is beneficial. Additionally, it speeds up building and reduces the volume of concrete ingredients that are wasted. Consequently, batching is a crucial step in the creation of concrete.
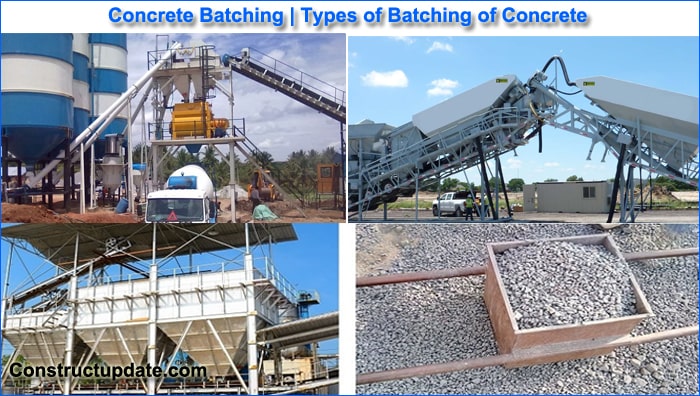
What Is Batching of Concrete?
To keep the consistency of the concrete’s quality, batching is the process and method of determining the volume of materials and combining them by volume and weight.
One of the most crucial factors in concrete batching is precision. Concrete is often batch-mixed by volume since it is more efficient than batching by weight. Before mixing begins, the aggregates and concrete components are correctly batched, resulting in accurate, properly batched concrete.
In general, concrete batching increases practicality because it facilitates the creation of a smooth surface and accelerates construction due to the volume of concrete being lowered for proper batching. Concrete batching is a crucial step in the production of concrete.
Types of Batching of Concrete
Before performing concrete mixing, there are three common methods of batching the ingredients for concrete. These are what they are:
Random Volumetric Batching of Concrete Ingredients
There is no proportion of cement, aggregates, water, etc. in random volume batching. It causes a mistake in the concrete, preventing it from achieving the necessary strength. The workers’ haphazard use of various containers makes it impossible to manage the amount of materials, and the number of containers is not taken into consideration.
Volume Batching of Concrete Ingredients
Another method of mixing concrete is called volume batching, which employs measuring boxes, also referred to as “gauge boxes” or “farms.” Typically, the volume of “farma” is 35 trash, or the equivalent of one bag of cement. Farmers then measure out all of the coarse and fine aggregates, and after everything has been correctly mixed, the project is complete.
Weigh Batching of Concrete Ingredients
The percentage of concrete materials is determined by weighing when batching concrete by weight (batching plant). Either “weigh batchers” or other suitable weighing methods are employed.
Weigh batching systems make accuracy, simplicity, and flexibility possible. Automatic batching machines are frequently implemented on major projects, which aids in obtaining the highest quality and consistency. There are various varieties of weigh batchers on the market, depending on the job. such as fully automatic weigh batching, semi-automatic weigh batching, and manual weigh batching (batching plant).
Importance of batching concrete
One must carry out the concrete mix design in order to create the long-lasting, affordable, and sustainable concrete (CMD). Concrete mix design is the systematic and scientific process of selecting the most cost-effective relative proportions of different ingredients from the material that is available to produce cohesive concrete with the desired workability at the fresh stage and the desired strength and durability at the hardened stage (CMD). learn more about the design of concrete mix (CMD).
Following concrete mix design, the initial task is batching the various components of concrete, such as cement, aggregates, admixtures, etc. Concrete is mixed in batches by weighing or mixing the necessary elements by volume according to the mix design.
Different Elements That Influence the Selection of a Batching System
The following are some of the several types of factors that affect the batching system.
One of the most crucial factors is the decision of batching, where you must select the batching strategy in accordance with your task location. Another crucial factor is the rate at which concrete is produced, and you should match your batching system to that rate. The typical batching process involves weighing the aggregates and batching.
Typically, weight watchers are managed manually or electronically. Despite the fact that manual weight batches are still used in some areas to conserve electricity, electronic weight watchers are more effective and prevalent in business nowadays.
While mechanical weight watchers use a circular scale and a spring to measure the aggregate weight, electronic weight watchers use an electronic scale and a hung load to measure weight. Compared to a manual scale, an electronic scale measures more precisely.
Weight watchers come in a variety of forms, and depending on the work, different forms are utilised, including low profile, high silo, subterranean batching plant, etc. Although most batches are fixed systems, some of them are moving and are regarded as transport vehicles.
Types of Concrete Batching Plants
There are typically three different types of batching plants, which are as follows:
- Manual Weigh Batching Plant
- Semi-automatic Weigh Batching Plant
- Fully Automatic Weigh Batching Plant
1. Manual Weigh Batching Plant
The first form of batching plant that was utilised in the past was the manual weight batching plant. This kind of plant requires a lot of work and requires poor proportion maintenance.
All of the aggregates are manually mixed in the manual weight-batching facility. Small-scale construction projects use a manual weight-batching plant.
2. Semi-Automatic Weigh Batching Plant
Another form of batching plant where the aggregate bin gates are manually controlled is a semi-automated weight batching plant. The gates are automatically opened during the mixing operation and shut after the delivery process is complete.
3. Fully Automatic Weigh Batching Plant
The most popular type of batching plant in recent years is a fully automated weigh batching machine. It is an automated system that requires the use of skilled engineers.
An automated microprocessor controls the batching system in a fully automated weigh batching facility. This device also measures the moisture content of the aggregates automatically. If the moisture content varies, relative measurements will be conducted to determine the appropriate strength of the concrete.