Stone Quarrying in Construction – Site Selection, Methods, and Equipment Uses
Stone extraction from natural rock beds is referred to as stone quarrying. The word “quarry” describes a location where various types of stones are extracted in an exposed state at or just below ground level. Stones collected in this way are employed in a variety of construction projects. In this article, we will try to understand stone quarry methods, site selection, equipment uses, and some crucial consideration points.
Site Selection for Quarrying of Stones
The following factors should be taken into consideration when choosing the quarry.
- The site should be close to populated areas where labor, tools, and other materials are always available.
- There should be at least one sort of transportation facility (road, rail, port, or all).
- Near the quarry site, there should be a source of clean water.
- There should be plenty of high-quality stone accessible.
- The site should be remote from permanent buildings like bridges and dams since blasting vibrations could damage them.
- There should be a non-living space available to dispose of the waste produced by quarrying.
- A suitable drainage system ought to be available.
- Reading the site’s geological information is recommended.
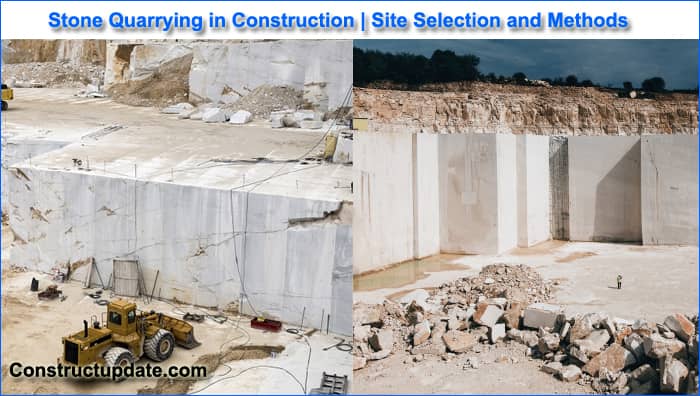
Crucial considerations before beginning a quarry
Examining and studying the rock surface:
Pay close attention to the outward open surface of the rock bed. Every instance of splits, gaps, and folds should be reported separately. Later, decisions for quick, safe, and affordable quarry operations can be made based on the results of this study.
Master Plan:
For a quarry to operate economically and for a longer period of time, a layout or master plan that details all phases of quarrying operations is essential.
Workforce and Equipment:
In order to get the most out of the quarry, there needs to be good cooperation, bonding, and coordination between the working people and the machinery utilized there. For instance, operating a machine without sufficient maintenance can result in an unexpected breakdown that impedes production and incurs additional costs. However, a competent worker who manages the machinery and does routine maintenance may produce goods quickly and earn a respectable amount of money.
Top surface removal:
Layered rocks, soft in nature, loose, and earthy material make up the rock that is acquired through top surface stone quarrying. Except in areas with valleys, where it can be used as a dumping material and a somewhat harder material can be used as a base course material beneath PCC, this material is not at all appropriate for any major construction activities.
Structural stability:
Take note that there should be no impact from the stones that were removed during stone quarrying. The sides of the building must be properly treated to maintain its stability. This includes creating suitable slopes with a minimal angle of repose (not to exceed a 45-degree slope), “Stone or Earth benching” at regular depths, and as much wider width as is practical to prevent land sliding with disastrous consequences.
4 Common Methods of Stone Quarrying
- Digging
- Heating
- Wedging
- Blasting
1. Digging
Stones are simply dug using the appropriate tools in this procedure. When soft stones are present in the earth at low levels, this strategy is helpful.
2. Heating
This technique involves heating the rock’s top surface. A dull bursting sound signals the separation of the upper layer of rock as a result of uneven expansion.
Next, the detached blocks are eliminated. When the rock structure is made up of thin, horizontal layers, this technique can be helpful.
3. Wedging
This approach is used if the rock surface has fractures or cracks. These cracks are penetrated with a hammer and steel wedges or points.
Then, with the aid of the proper tools, the stone blocks are moved and removed.
If there are no available natural fissures, artificial cracks are created. For relatively soft rocks, this approach is used.
4. Blasting
- In this quarrying technique, an explosive is used to break up the rocks into smaller pieces.
- When hand rocks without fissures or cracks need to be broken into little pieces, this technique is utilized.
- Since the stone obtained during blasting is often tiny, it can be utilized as road metal, railroad ballast, concrete aggregate, etc.
Quality of stones
Hard, long-lasting stones that are suitable for construction should be the standard for stones taken from quarries.
The quarry will most likely supply a sizable amount of stones.
Proximity of quarry
Favorable The state of the roads and the terrain for moving stones from the quarry to the crusher.
Stone quarrying’s proximity to roads, bus stops, cities, towns, etc., as well as its distance from transportation hubs.
Safe dump site away from residential areas and protected from any health risks for quarry workers.
To ensure that the blasting process may be completed without interruption, stone quarrying should be conducted outside of any neighborhood or area containing permanent structures.
Equipment and Machinery used in Stone Quarrying
Crawler tractors, bulldozers, mobile compressors, drilling and molding equipment, pulley blocks, belts, cranes, channellers, crushing hammers, saws, screens, tippers, dumpers, mobile vans, chain, personal safety gear, safety nets, supporting poles, planks, and mesh against earth sliding are some of the common construction tools.
Related Posts
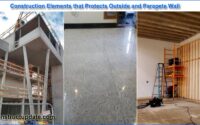
Construction Elements that Protect Upper Walls of a Building
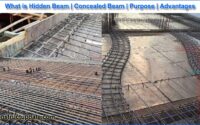
What is Hidden Beam or Concealed Beam | Hidden Beam Purpose, Application, Advantages
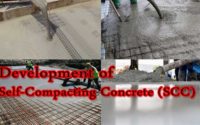
Self Compacting Concrete (SCC) – Development Overview
About The Author
I love to share my experience on civil engineering and construction estimates. As a highly capable individual with a strong academic background, I am proud to say that I already possess a comprehensive understanding of the technical elements of civil engineering.