What is Concrete Form | Different Types of Concrete Form
What is a Concrete Form?
A concrete form is a formwork system for reinforced cement concrete that includes strong thermal insulation. The concrete formwork is required to give the concrete a shape.
A novel concrete form technique has been created recently that adds extra features to concrete cast, such as insulation and surface pattern impact. Following are various types of concrete form:
1. Wooden Concrete Form:
Uses of Wooden Concrete Form
- When we need to lay concrete from any type of free-form design or any curves, we use a wooden form with a narrow cross-section.
- The wooden form is the most common and basic type of concrete form, and it is mostly used for casting concrete.
Advantage of Wooden Concrete Forms
The following are some of the benefits of using wooden concrete forms:
- The advantage of using wooden concrete forms is that they may be used to create any shape of residential construction.
- Another benefit of wooden concrete forms is that they are the most basic and traditional type of concrete form for casting concrete.
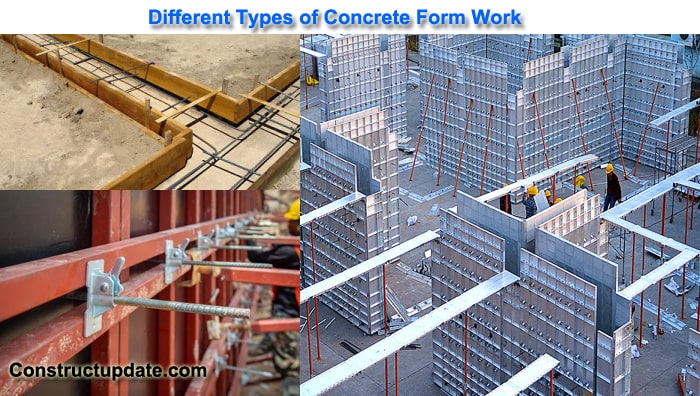
Disadvantage of Wooden Concrete Forms
Below are some of the disadvantages of using wooden concrete forms:
- The downside of using a wooden concrete form is that it cannot be utilised for a heavy concrete building.
- The most expensive concrete form is one made of wood.
2. Concrete Wall Forms
Pouring walls or larger structures, such as piers or foundations, requires the use of pre-fabricated concrete wall forms. Engineered wood with a metal frame or a fully metal body are the most common materials used in pre-fabricated wall systems.
These systems, also known as gang forming systems, are meant to use a set of latches or pins to attach and form a homogeneous structure. A tie is also used in pre-fabricated wall systems to hold reinforcing bars in place inside the wall form and to secure one section to another when the walls are being poured.
Prefabricated wall forms come in a wide range of shapes and sizes, with most manufacturers willing to make custom sizes for specific projects.
3. Insulated Concrete Forms (ICFs)
An insulated concrete form system is made up of a hollow block of insulating materials that fit together, which is then filled with concrete and strengthened with steel.
The foundation slab is used to construct ICF systems, and the system stays in situ to serve as both the foundation and the outside wall system. Following the installation of the insulating elements, a network of metal reinforced bars is installed inside the block wall structure, followed by the pouring of water-mixed or ‘high slump’ concrete.
ICFs are exceptionally energy efficient, and the foam-concrete sandwich is extremely long-lasting, making them ideal for usage as walls, roofs, and even floors!
4. Steel Concrete Forms
These are steel-based concrete forms. Steel forms can be kept consistent for up to 2000 work cycles if properly maintained and handled. As a result, when compared to wooden concrete forms, this is a better long-term building choice.
The steel forms do not absorb moisture from the concrete, resulting in fewer errors when the forms are removed.
How to Select Concrete Form for a Building Construction Project:
Intimately, there are a few crucial factors to consider when choosing strong forms, which are outlined below:
- Concrete forms can be purchased or rented.
- Before purchasing, consider the cost of ownership and its long-term utility.
- If renting the form is preferred, the most easily accessible and economical form is selected.
- The choice of form is influenced by previous experience with a certain sort of form.
- No output losses are projected if a form system is used, which is more familiar to workers.
- Losses are likely if the new form system is not properly trained.
- Steel forms provide a cleaner finish with fewer bug holes on the cast solid surface than wood forms in terms of aesthetics.
- When it comes to tolerance, steel kinds are a better choice than others.
- Internally, these forms are rigid and do not absorb moisture.
- For low-height constructions, wood forms are the ideal alternative.
- In comparison to wood forms, heightened steel forms with additional bracing and support are the best solution for longer forms of 20 feet.
- Steel forms are an effective alternative for casting concrete with straight, curved, or numerous offsets and abstract turns.
- Thin wood forms can be used if cost is a problem.